Pizza pan maker finds leaner methods create Green results
Lloyd Industries recognized for its innovations
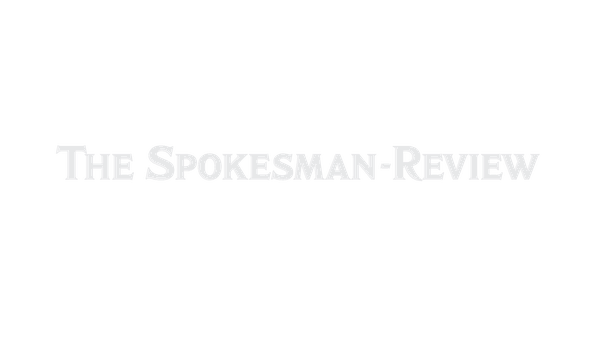
Tucked into the maze of bustling companies within the Spokane Business and Industrial Park, a once-small cookware manufacturer is rapidly becoming a green giant.
In an effort to make Lloyd Industries more streamlined and efficient, President John Crow has discovered that trying to be leaner can equal greener.
“I prefer ‘eco-friendly,’” he said during a walk-through of the company’s pristine manufacturing site.
It’s not often that busy production lines and warehouses are described as pristine, but Crow has found that keeping things as clean and tidy as possible really is part of an eco-friendly business.
For instance, you won’t find scraps of paper on the floor or empty soda cans lying around this sprawling 40,000 square foot facility. Just about everything is recycled or re-used, from paper products to energy – the production machines even help heat the facility.
And now, what began as a part-time pizza pan-making business has grown into “the largest pizza pan maker in the country,” said Crow. “We sell to 50 of the top 100 pizza franchises.”
The company’s market now extends into Canada, Mexico and Europe. As the company’s reach has expanded, so has the product line: Lloyd now manufactures commercial cookware and bakeware in addition to pizza products.
To Crow’s delight, as production became more streamlined, he saw his business became more environmentally-friendly as well.
“Lean means you eliminate waste in manufacturing,” he explains.
So what makes Lloyd Industries so green?
* Recycling: “We recycle everything,” Crow said – and he’s not talking just about pop cans. All scrap metal from aluminum to stainless steel is sorted, separated and sold to a local scrap-metals dealer. Also recycled are office paper, cardboard, and even the paper separating sheets of metal.
One of the more unusual ways Lloyd Industries recycles is in its own wastewater treatment line. The company reduced anodizing water consumption and wastewater generation from 2,000 gallons per day to about 300 gallons.
It also sends alum derived from this process to the city of Spokane’s wastewater treatment plant, which city officials say helps the settling process in the treatment plant’s clarifiers.
* Energy Consumption and Savings: More than 60 percent of Lloyd Industries’ electricity is derived from renewable hydro and wind power with the balance coming from natural gas. To save heating costs, Crow made sure the building was well insulated, and installed fans in the rafters which direct warm air down to the floor. More warmth is supplied by excess heat from the machinery.
* Eco-friendly products that reduce energy consumption: “We’re not only green in our factory, we’re making the restaurants green, as well,” says Crow.
Traditional commercial cookware often features nonstick coatings that are kerosene or solvent-based. These types of coatings can flake off and leach into food. Metal utensils can’t be used on this type of cookware because it scratches so easily. Pans with this toxic, nonstick surface can’t be recycled, either.
Lloyds’ chemists and engineers devoted several years to developing innovative water-based nonstick coatings they have dubbed, PSTK, short for Pizza Dura-Kote, for bakery use, and TK7 for cookware use.
Pans featuring these coatings need minimal oiling, making them more consumer-friendly. The surface is hard enough to withstand metal utensils with no scratching or flaking. Crow said it’s 30 percent harder than stainless steel, which means food cooked with these products will retain its integrity and flavor.
He said Lloyd’s products feature Type III anodizing, which fuses a ceramic-like hard shell directly onto the bakeware, producing a surface so durable that company literature said “is specified by NASA for heat shield components on the space shuttle.”
The results for users are products that heat up extremely fast and use less heat to cook. Less cooking time results in less energy. The pans are also easy to clean, requiring less hot water and detergent. They’re also amazingly lightweight which saves on shipping costs and fuel usage. The pans are extremely durable. Crow says, “You never need to get rid of a Lloyd pan.”
* Transportation: Crow says, “We’re the only plant with our own in-house anodizing line. Everyone else ships (their pans) out.”
The facility is completely self-contained. “We don’t waste a lot of energy moving things back and forth.”
Lloyd Industries also saves on fuel costs by having employees work four 10-hour days. The company currently employees 20, and one employee works from home. In the future, Crow said the company hopes to have more workers take advantage of telecommuting.
“We try not to waste anything — including people,” he said.
The company’s efforts haven’t gone unnoticed. The City of Spokane, Spokane County and Washington Department of Ecology have all praised the company’s efforts.
Stella Matei, pretreatment engineer for Spokane County department of utilities, said Lloyd Industries is probably the county’s is best industrial user.
“Lloyd strives to do things right. They’re very environmentally conscious,” she said.
In a letter to the company, Rolfe Parsloe, Hazardous Waste Technical Assistance Specialist for the Washington Department of Ecology, called the wastewater effort “Lloyd’s most impressive accomplishment,” and added that the company is “one of the most progressive of the 500 or so companies I have visited during the 12 years I have worked for Ecology.”