Computer engineers in CdA design new reusable mask for medical uses
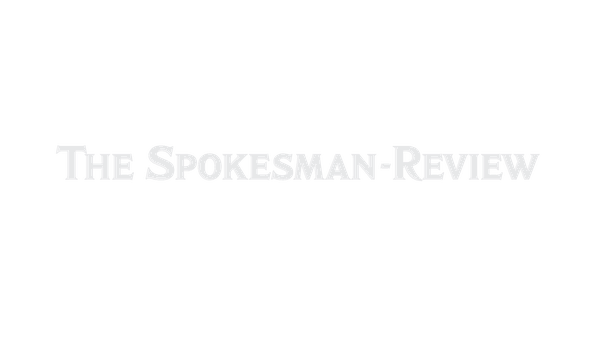
Computer engineers from Coeur d’Alene are teaming up with a Liberty Lake manufacturer to turn their expertise of making high-strength aircraft components into reusable N95 masks that could help ease the shortage of protective equipment needed by medical personnel, essential employees and first responders during the coronavirus pandemic.
Continuous Composites CEO Tyler Alvarado and his team designed the masks with their patented technology, which uses computer programs to tell a robot how to build something. His team then worked with professionals at Kootenai Health, who helped test the models to see how they fit.
They now have a mask built with a type of flexible rubber that is form-fitting so it fits different face shapes , including those of people who couldn’t previously wear standard N95 masks.
The prototype can be sterilized and reused, and can be mass produced if the demand remains strong.
“I’m extremely excited with the progress we have been able to make in such a small amount of time,” Alvarado said. “We were trying not to operate in fear. We had to protect our business and our community. But we wanted to take it a step further and be part of the solution.”
Rick Taylor, vice president of Altek in Liberty Lake, said he has worked with Alvarado’s company on multiple projects. Altek manufactures all kinds of equipment for the medical, aerospace and diagnostic fields.
“When we saw the design, we offered some enhancements for manufacturability,” Taylor said. “They liked what we offered, and the rest is history. We are cutting steel right now for injection molds for these masks.”
If all goes well, production should start within a couple of weeks. Once the first masks are produced with Altek’s injection molds, they will go through another round of test fits with medical personnel before full-scale, 24-hour production is launched, Taylor said.
“What is gained from these masks is the comfort level,” he said. “Not only does it offer a better seal than the standard N95 masks, but it’s also comfortable as well.”
The initial molds would daily make about 2,000 small- and 2,000 medium-sized masks, which would fit more than 90 percent of users. If everything checks out, Altek will then build what’s called “multicavity molds” that can make eight times as many in 24 hours. Those numbers climb as each multicavity mold is added.
“We are doing preproduction just to get the product out as quickly as possible,” Taylor said. “With our experience of both market demand and flow characteristics of the material, then we’ll decide how many multicavity molds we want to build.”
Alvarado said his staff reached out to Idaho Gov. Brad Little in March and asked how his engineers and his company could help. Alvarado said he met with mechanical engineer Andrew Overby on March 27 to figure out what they could offer. Two days later, they decided to design the reusable masks.
“That’s when we looked across the table and said, ‘Let’s go for it,’ ” Alvarado said.
Overby said Continuous Composites, which was founded by Alvarado, John Swallow and Ken Tyler, could have tried to do everything on their own. But there was no need.
“We are the main contributors to the design,” Overby said. “We realize there is a ton of other talent out there in our community. We are just blessed that this community has people willing to put in the effort and get this stuff out the door.”
In addition to Altek, Alvarado said he also reached out to Craig Dolsby, who owns True Seals in Spokane Valley. Alvarado said Dolsby has already started making 16,000 clear-plastic masks a day that doctors can wear all day to prevent the spread of the coronavirus.
“We were looking for manufacturing capability for elastic bands,” Alvarado said.
True Seals also has a computer numerical control, or CNC, machine that can cut out thousands of filters at a time from rolled material, he said.
In addition to providing for medical use, Continuous Composites plans to launch a website where members of the general public can preorder the masks, marketing manager Allie Hambling said.
“I am so proud of our team and what we have been able to accomplish,” Alvarado said. “By leveraging the broader team and the relationships we have in the community, together we can conquer whatever we set out to do.”