Suit factory evolves to survive
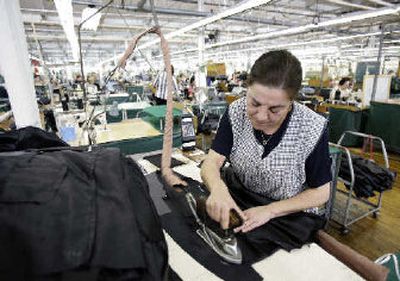
NEW BEDFORD, MASS. – The two might seem as unlikely together as a hand-stitched double-breasted suit jacket with a pair of work pants: Anthony Sapienza, the son of a factory manager, and Warren Pepicelli, who grew up on the union side, pounding the pavement as a business agent in Boston, walking from one of the city’s 60 women’s garment factories to another.
But Sapienza, president of the Joseph Abboud suit factory, and Pepicelli, who runs its union, are working hand in glove. Union and management are collaborating to revamp timeworn garment-making methods in favor of manufacturing techniques pioneered at Toyota Motor Corp. Their goal: Survival in the face of cheaper foreign competitors.
The U.S. garment manufacturing industry has bled jobs for decades, as work moved first to cheaper labor in Mexico, then to Asia. As Chinese manufacturing becomes increasingly skilled and sophisticated, the few U.S. factories that remain are vulnerable, and their managers know it.
Sapienza and Pepicelli both have about 30 years in the business. Sapienza, who spent his boyhood Saturdays sweeping cuttings in his family’s menswear factory, then wrestling his brother in the pile of scraps, remembers when there were 40,000 U.S. workers making men’s clothing. Now there are 4,000, he said.
For Pepicelli, the days when he could stand on a street corner in Boston and look up at row after row of women sewing in second-floor factories are just a memory. Every one of those factories is closed.
That’s what everyone at Abboud’s sprawling skylit brick factory, built as a cotton mill around the time of the Civil War, is working to avoid. And if anyone forgets what’s at stake, they need only drive down the street, where the Cliftex menswear mill that used to employ more than 2,000 workers sits, its windows boarded.
Abboud has hired the best workers from its failed neighbors, managers there say. The city lost 67 percent of its manufacturing jobs during the 40 years ending in 2000, according to the Brookings Institute. For many of the factory’s workers, Sapienza said, “This is the one opportunity they have to continue to work.”
The push for change comes from Marty Staff, president and chief executive officer of JA Apparel Corp. Staff and private equity company J.W. Childs bought the company in 2004; the brand’s founder, Joseph Abboud, left in 2005.
“If you said, ‘Let’s create a half-million-square-foot facility in the U.S. and hire 600 skilled workers to make high-quality garments,’ you could never do it,” said Staff. “It would be like building the Holland Tunnel.”
Abboud says its sales are about $400 million a year. While the company is doing fine, management says the U.S. factory has to improve constantly to justify the higher salaries its workers make compared to foreign competitors. The average wage in the factory is $12 an hour, plus union benefits. That’s three or four times what workers in Mexico make, Sapienza said.
But if the workers in New Bedford could make suits faster, the advantages would be even greater. Then the company could restock a successful style at stores in season – it could get fresh winter suits to shoppers in late January, for instance, if a store had run out of a size or a color. It could introduce the “fast fashions” that stores like H&M and Zara sell – edgier styles that arrive every month, then are swiftly replaced.
So far, there are only three teams, each with eight to ten workers, at the 600-person factory. The company hopes to move one-third of its jacket production to teams by August and all trouser production to teams by September. That switch would be enough to keep up with seasonal reorders and custom suits, Sapienza said.
For now, most of the factory’s work is still done on the piecework system, which hasn’t changed since the 19th century. A worker will take a tied-up bundle of, say, 20 sleeves, untie them and perform a single task on each sleeve, such as pressing the seam. Once she has completed her work on all the sleeves, she will re-bundle them, load them in a cart and roll them to the next worker, who will unbundle the sleeves, complete her one task on each sleeve, re-bundle them and roll them along.
Individuals are paid by the number of pieces they complete, with a guarantee they’ll make minimum wage, plus 25 cents an hour. “Make more, get paid more,” Sapienza said. Most do; hence the average wage of $12 an hour.
The average wage on the teams is still $12 an hour, plus benefits, and there are shared bonuses if the team beats its quota, or makes its quota faster. Individuals with additional skills, or those who have trained to do more than one job, are paid a higher wage. The hourly goals are laid out on a chart near the team. A green dot by an hour means the team has hit its goals, a red dot means it’s missed.
Gabriela Rodriguez, 50, of New Bedford, has been working in garment factories for 28 years, 10 of them at Joseph Abboud and is on the first team the company started. She likes it, she said. “I’m not under the pressure of piecework.”