Go inside Texas Instruments’ newest fab, where chips powering the digital world are born
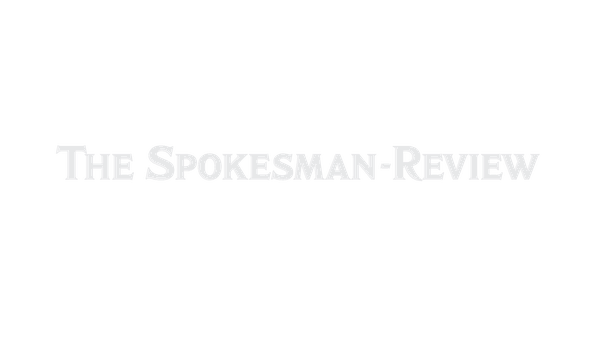
Texas Instruments’ new silicon wafer fabrication facility in Richardson, Texas, could easily be mistaken for a typical business expansion. It’s been built to blend in with an adjacent structure that’s been part of the company’s manufacturing arsenal since 2009.
But inside, four shifts of workers wearing white safety suits that resemble hazmat gear move around the clock through the 630,000-square-foot combined clean room space. This sterile environment is where a 400-step process takes place to turn 300 millimeter wafers into some of the world’s most essential technology.
Specialized pods that can weigh the equivalent of three gallons of milk carry production materials around 15 miles of track connecting the two factories. That allows the facilities to operate independently but still work together in unison.
The new plant, known as RFAB2 in Texas Instruments’ parlance, is the company’s latest addition to a global manufacturing footprint that produces billions of analog and embedded processing chips for some 80,000 products. Cars, calculators and industrial machinery all use TI chips.
It also represents TI’s role in an industrywide effort to bring more chip-making to the U.S. – a necessity driven home by pandemic-era supply shortages. By 2025, the first fabrication facility in TI’s planned $30 billion, four-fab investment in Sherman could be producing chips as well.
Setting the stage for success
RFAB2, which began production in September, is 30% larger than TI’s original fab and took two years to complete.
The company is actively hiring as it ramps up production, said Kyle Flessner, TI’s senior vice president of technology and manufacturing group. TI’s job board has 268 openings posted in Richardson as of Thursday.
The fab will eventually employ 800 workers, some of whom will come from TI’s college program.
“We have a very robust internship and new college grad program,” Flessner said. “We leverage that for the majority of our hires.”
TI hires over 1,000 interns every year, and some are invited back or asked to join one of its full-time rotation programs. The company likes to hire candidates with technical backgrounds, which can mean degrees in electrical, mechanical or chemical engineering.
“Earlier career talent is looking to have multiple experiences,” said Brian Dunlap, TI vice president of the 300 mm wafer fab manufacturing operations. “We’re trying to create that work environment … and it’s helping the factory grow.”
The significance of analog chips is key to understanding TI.
Analog chips change real-world signals, such as sound, temperature, pressure or images, into streams of digital data that can be processed by other semiconductors, such as embedded processors, according to a company filing.
“Analog is how we interact with the real world,” Dunlap said. “It allows us to be able to connect to the senses through digital processing in how our chips allow us, as humans, to interact with the world of electronics.”
Embedded processors can be used for combinations of performance, power and cost, acting as a “digital brain.” The Richardson fabs don’t produce embedded processors, though it’s an important business line for TI.
In 2021, TI’s analog division generated over $14 billion in revenue. Embedded accounted for over $3 billion of the company’s $18.3 billion in total revenue.
Industrial and automotive are two of TI’s core markets and made up 60% of its sales last year.
“Our industrial and automotive customers are increasingly turning to analog and embedded technology to make their end products smarter, safer, more connected and more efficient,” TI head of investor relations David Pahl said on a call with analysts earlier this year.
Electric vehicles, for example, can require three times as many chips as gasoline-powered cars and trucks, Flessner said.
Factory automation drives a lot of TI’s industrial business.
The future
Nearly every device that plugs into a wall or contains a battery has a TI chip, Flessner said. Worldwide, the firm has 15 manufacturing sites where tens of billions of chips are produced each year.
Before semiconductors can roll off a line and into products, fabrication plants start with a large, mirrorlike sheet of ultrathin silicon that yields thousands of chips. The Richardson fabs work with 12-inch wafers that are 300 millimeters in diameter.
From those wafers, the combined Richardson fabs are expected to crank out more than 100 million analog chips a day.
TI’s history runs deep in North Texas, spanning more than 90 years and including Jack Kilby’s 1958 invention of the first integrated circuit. Its corporate headquarters is prominent at the intersection of U.S. Highway 75 and Interstate 635 in Dallas, and other company operations dot the local landscape.
“What we get through placing scale in the North Texas area is a greater infrastructure to support our manufacturing needs,” Flessner said.
The new Richardson fab brings the company’s 300 mm wafer facilities to four.
Last year, the company added a Micron Technology Inc. semiconductor factory to its portfolio in a $900 million deal. That plant in Lehi, Utah, began producing analog and embedded chips this month.
Construction began in May on the first of the four new fabs planned for Sherman. If all four are built, it would expand TI’s production capabilities to eight 300 mm wafer fabs.
The company’s selection of Sherman a year ago has since spawned other semiconductor-related investment around it.
In June, GlobiTech selected the North Texas city for a new $5 billion plant that will produce silicon wafers. The subsidiary of Taiwan-based GlobalWafers Co. will create 1,500 new jobs. This week, Finisar said it is considering putting a $3 billion silicon wafer plant on its existing Sherman campus where it makes the specialized lasers in Apple’s iPhone facial recognition technology.
“We obviously believe strong companies produce strong communities and strong communities help produce strong companies,” Flessner said.