Former pilot reduces cost, weight of hydroplanes with composites
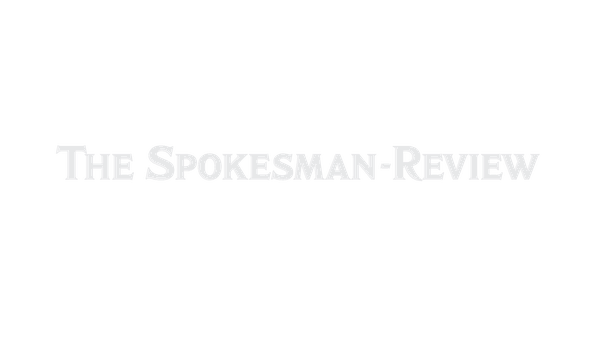
Murdo Cameron has something to tell the sport of hydroplane racing: Lighten up already.
The retired airline pilot, an innovator in the field of advanced composite materials, says he can transform how thunderboats are built, greatly reducing their weight and cost while making them stronger.
And he’s well on his way to proving it at an aerospace school near the Coeur d’Alene Airport.
“I think it’s a revolutionary breakthrough in building unlimited hydroplanes,” Cameron said.
Working out of the new Aerospace Center of Excellence at North Idaho College, the 69-year-old native of Wallace is making carbon fiber-reinforced resin hulls cast from the molds of existing hydroplanes. Instead of fabricating scores of smaller parts that need to be assembled, he can produce a hull in just three big parts: a single bottom and two top pieces.
The result, Cameron said, will be a boat that is far lighter and more resilient than those now competing around the Northwest and elsewhere, traveling up to 200 mph.
He envisions a new generation of hydroplane hulls made in North Idaho.
“We’d like to build the highest-tech, fastest boat in the world right here in Coeur d’Alene.”
The sport is hurting for new equipment, Cameron said. “They don’t have enough hydroplanes out there to put on really good shows.”
Few new boats race on the H1 Unlimited circuit, confirmed Mark Evans, a longtime hydroplane driver and owner of Evans Racing in Chelan, Washington.
“We’re all running 30-year-old technology out there,” Evans said. “Even though our boats look like the Space Shuttle … structurally we’re still behind. And a lot of them are so beat up, you know, they keep falling apart and are getting heavier and heavier because we keep adding weight. To have teams with new hulls would be really cool.”
He was so intrigued by Cameron’s work that Evans let him borrow one of his hulls as a master for the new molds. Using that boat and another on loan from Leland Unlimited of Kirkland, Washington, Cameron has made composite parts for two unlimited boats plus one display boat.
Ideally, this new approach will cut by half the weight and cost of the hulls as well as the time it takes to build them, Evans said.
A standard new hull today would set an owner back $250,000 to $300,000, he said.
Another advantage of this method of manufacturing is it simplifies the repair process, allowing teams to get back out on the water faster after a crash, he and Cameron said.
“If I knock a hole out of the boat that was built in this mold, I can go in and make that part and plug it back into the boat,” Cameron said. “That’s kind of unique.”
With support from Airtech International Inc., which makes materials for the resin infusion process, he can make complete parts in 45 to 90 minutes. That includes the massive bottom hull piece measuring around 426 square feet.
“The carbon fiber runs from one end to the other end. It’s a continuous element,” he said. “It is the future of composites. It’s fast, it’s clean.”
Cameron, who once flew Boeing 767s and now serves on the NIC aerospace center’s advisory board, also wants to pass along his expertise in advanced composites.
One possibility, he said, is a short course through the NIC Workforce Training Center in Post Falls.
He has worked with ultra-strong, versatile composites for years.
He built a full-size replica of the P-51 Mustang, a World War II-era war bird, using graphite composites.
More recently Cameron used the technology to replicate the Miss Spokane, a vintage unlimited hydroplane that raced in the late 1950s and early ’60s.
Cameron said he hopes his process will allow new teams to enter hydroplane racing.
He also thinks it will enable owners to afford a second hull as a backup in case the primary one is damaged – a competitive advantage that can attract bigger sponsors, he said.
With just one boat, “You go out and run two races and wreck this thing, what are you going to do for the next five races? You’re out of business,” he said.
One question Cameron already is getting is whether a much lighter hydroplane is more prone to fly up out of the water. He talked with industry veterans about this and said he learned the key factor in preventing blowover is the skill and experience of the driver.
The lighter hulls also complement a growing interest in new power sources for hydroplanes, such as automotive engines.
The boats racing today use turbine engines from Vietnam War-era helicopters, but team owners are finding those in short supply.
“Right now these turbine engines that we run are very expensive and the parts are very hard to get,” Evans said.
He believes the V8 engine is the next big adaptation for the sport, with the potential for sponsorships by major automakers. Piston power packs less horsepower than turbine engines but may be able to compete in a lighter boat, Evans said.
He’d like to be out on the water next summer with V8 engines, hopefully in one of the new hydroplane hulls from Cameron’s shop.
“I’ve dealt with turbines – I’m done,” Evans said.
“I actually want to put two big V8s in with a multi-speed gearbox and try to kick the turbine’s butt. A lot of people don’t think it’s possible, but with the technology now, a lot of people are starting to think it is.”