Spokane’s Bill Howland is bowyer par excellence
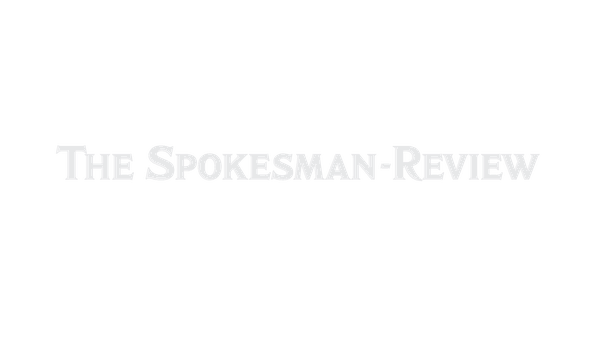
There is a three-year wait-list for a bow made by Spokane resident Bill Howland of Brackenbury Custom Bows. Some customers on the list aren’t even sure yet what bow model or wood they want. They just know they want Bill to build it.
Howland purchased Brackenbury Custom Bows in 2001. The company’s founder and original bowyer, Jim Brackenbury, created what some consider some of the finest traditional bows. His nephew continued the business after his death, until Howland offered a proposition – to not only continue Jim’s legacy, but to build on it.
For his first seven years, Howland worked seven days a week, 12-15 hours a day, until his wife politely asked him to ease up a tad.
“We don’t make very much money in this business,” Howland said. “It takes a lot of time to build bows. Takes a lot of time to service these customers. I get a lot of phone calls in a day. … I have customers that travel great distances – from England, Germany, France – to come and want see what I do and how I do it and why I do it the way that I do it.”
Every bow Howland creates begins as blocks of wood. The only manufactured material he orders in is fiberglass to layer among the wood in the limbs. Everything else is cut, grinded, sanded, sprayed, assembled and tested for quality by Howland.
Customers can customize everything in the model they choose – from the length of the bow to the draw weight to the wood used for the riser, limbs, veneers and accents. It is a balance of both beauty and efficiency, especially since certain woods cast an arrow better than others. Next, Howland asks customers to send an outline of their hand. The lifeline of an archer’s palm should align perfectly with the grip of their riser, he believes.
“Just in assembly of the actual bow itself, without getting it where I can put a string on it, can take me close to three weeks,” he said. “I got to cut the cores, grind the cores, got to cut veneers, grind the veneers, down to 18-thousandths thick. It can be a month just doing nothing but getting ready to tiller it.”
Howland works from the basement of his home just north of Spokane. He takes no shortcuts in his work. Some other bowyers might consider some of his methods less efficient, but Howland knows better – quicker doesn’t mean better.
For example, he doesn’t create the upper and the lower limb of the bow at the same time. He uses only one form for both.
“Because how hard is it to make too exact forms perfect every time? It’s almost impossible,” Howland said.
“It’s like a house – if your foundation is off, your peak is going to be off, too.”
While a custom-made bow can take weeks to build, the process doesn’t end there. Howland must tiller the limbs, in order to make certain the limbs are timed correctly.
“Shooting a bow that makes a wavering sound, instead of a concise thud, means the limbs are not timed properly,” Howland said. “They may look straight on the rack, but at full draw, they could be off-kilter.”
In addition to a craftsman, Howland is a teacher. The lessons he offers are free.
He puts his students so close to the target they can’t miss. He tutors them on the fundamentals, perhaps having them close their eyes to focus on a proper three-finger release, what he calls “wiping the face.” Once they’re confident enough with that, he takes them back far enough to find “point-on.”
“With a bow, shooting instinctively, everything is out there in front of you. … It’s like a baseball pitcher, knowing where to release the ball to get it the catcher’s mitt. You got to learn the arrow flight.”
Howland also strives to be a mentor to future bowyers.
“I get a lot of calls from guys throughout the year that want to learn how to build bows. … I don’t think there should be trade secrets. If we want traditional archery to keep on going, there can’t be secrets.”
Howland, a traditional archer and hunter to the core, believes a life worth living is one filled with challenges, even when it comes to choosing a bow.
“Challenge yourself physically,” he said. “You can always work into a bow, if it’s a little bit heavier for you, unless you have a physical condition preventing from doing so. Always work up.
“I could have kept building just Jim’s designs. I challenged myself to develop other designs for other uses. It’s a challenging world. We can’t stay stagnant.”